Time to read: 6 min
Medical injection molding lets designers prototype and manufacture a wide range of products for the medical, dental, healthcare, and pharmaceutical industries. Some products, such as catheters, are tightly regulated. Other products have fewer requirements or are subject to regulatory guidance, such as wellness items. There are also injected molded parts (e.g., gaskets) that are not medical devices but must comply with material testing standards.
This article describes what you need to know if you’re ready for medical injection molding. Keep reading to learn about medical device classes, prototyping and scale-up, material selection, and tooling. You’ll also read about two medical device companies that leveraged Fictiv’s design for manufacturing (DFM) assistance and manufacturing network to accelerate new product introduction (NPI).
If you can’t wait to get started on your own project, create a free Fictiv account and request a quote.
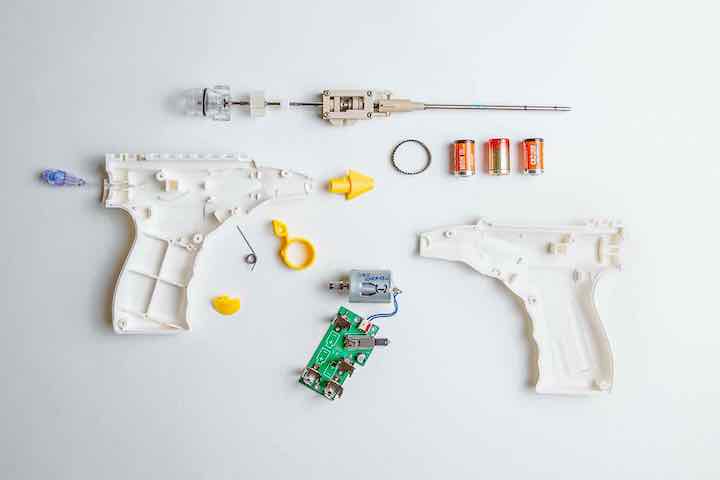
Medical Device Injection Molding
For designers, it’s important to approach medical injection molding with a clear understanding of what constitutes a medical device and the class to which it belongs. Otherwise, you risk making decisions that could delay NPI and incur unnecessary costs. For example, did you know that the U.S. Food and Drug Administration (FDA) classifies a manual toothbrush as a Type 1 medical device? Yet it’s also 510(k) exempt, meaning it doesn’t require extensive testing or premarket notification or approval.
Medical Device Classes
Both the FDA and the European Union (EU) Medical Device Regulation (MDR) divide medical devices into three classes. Class I devices are the lowest risk and Class III devices are the highest.
- Class I medical devices are not intended to support or sustain life and will not present an unreasonable risk of illness or injury to a patient. Test tubes are an example.
- Class II medical devices need to provide reasonable safety and effectiveness. Contact lenses are an example. The EU MDR also defines medium-risk (IIa) and high-risk (Class IIb) devices.
- Class III medical devices are usually designed to sustain or support life and may present an unreasonable risk of injury. Implantable prostheses are an example.
Before you get started, you need to determine which class (if any) describes the part or product that you plan to injection mold. In addition to regulations, do you need to consider any of these quality standards from the International Standards Organization (ISO)?
- ISO 13485 – Medical Devices
- ISO 10993 – Biological Evaluation of Medical Devices
- ISO 14644 – Cleanrooms & Associated Controlled Environments
In short, make sure you know which requirements you need to meet so that you can avoid doing too much or too little, both of which can cause unnecessary delays.
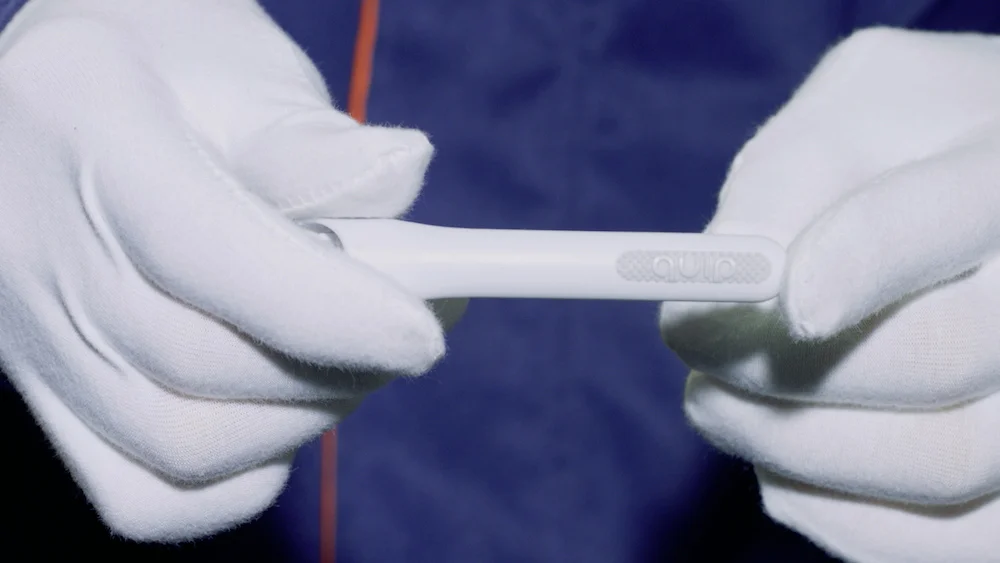
Medical Device Prototyping and Scale-Up
Once you’ve determined your FDA or EU MDR pathway, you’ll have some important DFM decisions to make. That’s where Fictiv can help. For prototyping, you could use 3D printing, injection molding, or both. But what if you can’t 3D print the same material that you plan to use during injection molding? How will this affect your test plan and compliance efforts? Then, when it’s time to scale up, will you need to change your design because it’s not ready for injection molding?
You could also bypass 3D printing and use prototype injection molding directly. This form of rapid injection molding is faster and less expensive than you might think. Regardless of the path to production you take, bridge tooling also provides a way to move from low volumes to high volumes.
Scaling Up to Medical Device Manufacturing
3D printing supports intricate part features, some of which are difficult, expensive, or impossible to achieve with injection molding. However, some features that can be 3D printed come with added costs and longer timelines. Other part features, such as lattice-like structures, can’t be injection molded at all. Plus, you won’t be able to use the same computer-aided design (CAD) when going from 3D printing to injection molding.
To assess your injection molding readiness, ask yourself the following questions:
- Are you using the right wall thickness and using ribs and gussets for support?
- Are you using large enough radii to avoid voids and warping?
- Did you round sharp corners, or use fillets, to facilitate mold release?
- Did you add a draft angle that’s large enough to avoid part damage?
- What is the part’s surface finish, and does it follow SPI guidelines?
- What is the allowable amount of flash?
- Do you need to adjust part tolerances?
Check out Fictiv’s checklist to know when you’re ready to go from 3D printing to injection molding. Even better, download Fictiv’s Injection Molding Design Guide. This free resource explains all of the concepts in our checklist along with what you need to know about designing parts for injection molding.
Download the Injection Molding Design Guide
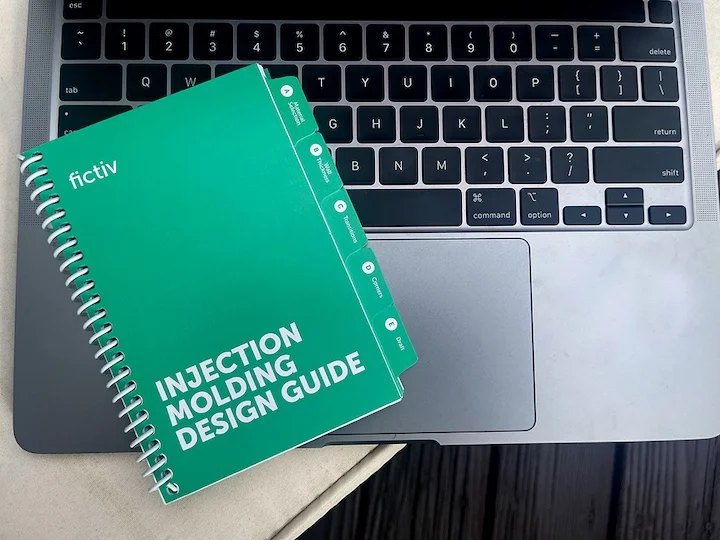
Medical Injection Molding Materials
Medical injection molding uses many of the same materials as other injection molding applications. However, medical products may need rubber or plastic materials in grades that meet specific testing standards. For example, USP Class VI silicones are safe for contact with human skin. You could use silicones that meet ISO-10993 testing requirements instead, but these materials tend to be more expensive and might be more than you really need for a medical device that isn’t implantable.
Commonly medical injection molding materials include thermoplastics, elastomers, and thermoplastic elastomers. Here are some examples that Fictiv supports.
- Polyethylene (PE) absorbs little water and maintains its structural integrity during multiple sterilization processes. Applications include membranes for oxygenators.
- Polypropylene (PP) provides excellent fatigue resistance. Medical injection molding applications include the living hinges on pill organizers.
- Polystyrene (PS) supports sterilization by radiation and is available in clear grades that are a good choice for blood dilution lab vials.
- Polyetheretherketone (PEEK) is an engineering thermoplastic with excellent mechanical strength that is used in load-bearing implants such as spinal cages and knee replacements.
- Thermoplastic elastomers (TPE) combine softness with elasticity and are used in medical bandages and tourniquet bands.
Silicone elastomers are also used in medical injection molding. They include both high consistency rubber (HCR) and liquid silicone rubber (LSR) in grades with FDA approvals. If you’re ready for injection molding, which material will you need?
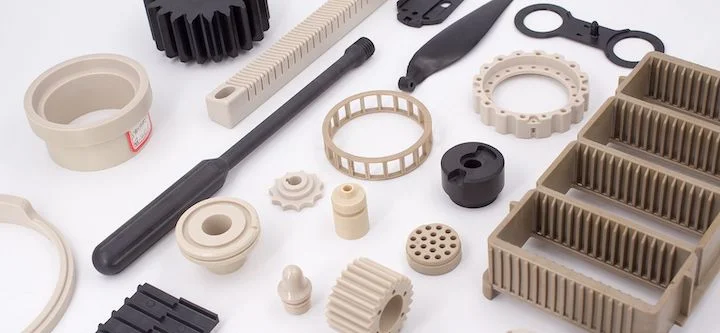
Medical Injection Molds
Fictiv gives you a choice of tooling materials for medical injection molds. Typically, prototype and low-volume injection molds are made of aluminum, softer steels, or semi-hardened steels. Aluminum is the least expensive metal and the easiest to machine, but it can’t match steel’s tighter tolerances. When it’s time for high-volume production and tight-tolerance parts, hardened steel is the right choice.
Ideally, a production injection mold is designed and built for the fastest cycle times, the highest quality parts, and the longest tooling life (i.e., cycles). For prototype injection molds, long tool life is less important than part quality, especially for first article inspections (FAIs). Cycle time is also less important, at least if you aim for low volumes like 100 representative pre-production prototype parts.
Medical Device Success Stories with Fictiv
When TransMed7 needed to iterate prototypes quickly and scale production seamlessly, they leveraged Fictiv’s 3D printing and injection molding capabilities. TransMed7 cut NPI from 10 to 2 years and developed five new breakthrough medical devices. The savings in infrastructure and overhead costs were worth millions of dollars.
Quip, another medical device company, used 3D printing and injection molding services to get up and running in just four weeks. Other manufacturers told the oral care company that it would take as long as eight weeks just to get the first off-tool parts. As one of Quip’s industrial designers explained, working with Fictiv was “a pace that I’ve never really experienced”.
Are you ready to take the next step? Create a free Fictiv account and request a quote.