Time to read: 4 min
3D printing, an additive manufacturing process, has made its way into almost every industry. From automotive to fashion, it has improved the way companies in a variety of fields do new product development.
However, long before 3D printing revolutionized prototyping, CNC (computer numerical control) machining dominated the manufacturing world. If your job is to design or develop physical products, CNC machining, a subtractive manufacturing process, is likely a part of your prototyping process. And, making the switch from 3D printing to CNC machining may be simpler and more beneficial than you think.
To manufacture a successful product, it’s important to understand these two foundational manufacturing technologies and how to best utilize each of them for different stages in your development cycle. In this article we’ll share guidelines around the best use cases for both 3D printing and CNC machining, along with a checklist to help you know which technique is right for your next project.
When to Use 3D Printing
3D printing continues to revolutionize hardware development by giving individuals and enterprise teams alike access to quick and affordable prototypes.
With 3D printing, teams can iterate on designs daily at a fraction of the cost of other prototyping methods. Additionally, constraints on part manufacturability are much lower with 3D printing as compared to CNC machining — so, teams can focus solely on moving from digital to physical quickly early on while the design is still evolving.
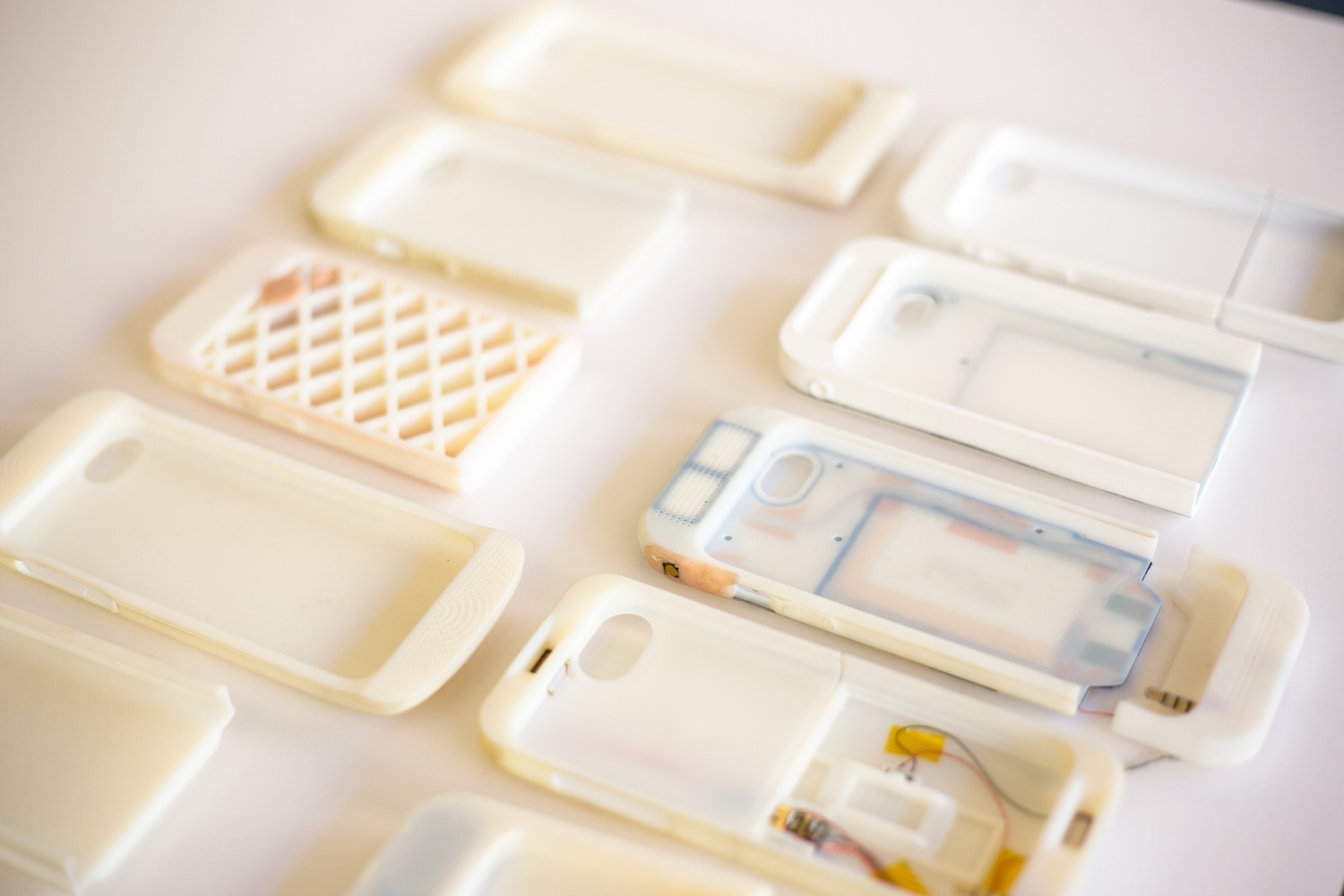
Here’s an overview of the best use cases for 3D printing and some pros and cons to consider:
Best Uses for 3D Printing:
- Early stage prototyping for fit and form
- Pre-manufacturability prototyping
- Ideal volume: 1 to 5 units (anything more may become costly)
Pros of 3D Printing:
- Fast production times
- Can quickly incorporate user/engineering feedback
- Ability to print complex shapes at a low-cost
- Makes polished-looking visual models
Cons of 3D Printing:
- Part assembly/functionality may not be exactly the same as the final product
- Tight tolerances aren’t always achievable due to 3D print resolution
- Not as appropriate for very high strength, functional applications
- Limited material options (3D printing plastic prototypes is common)
When to Use CNC Machining
CNC machining is a more traditional way to produce parts by means of subtractive manufacturing (i.e. taking a volume of material and chipping away at it). In considering CNC machining prototyping vs 3D printing, there are benefits of both. It takes longer to CNC machine a part than to 3D print one, but the final production quality and finish is generally superior with CNC machining.
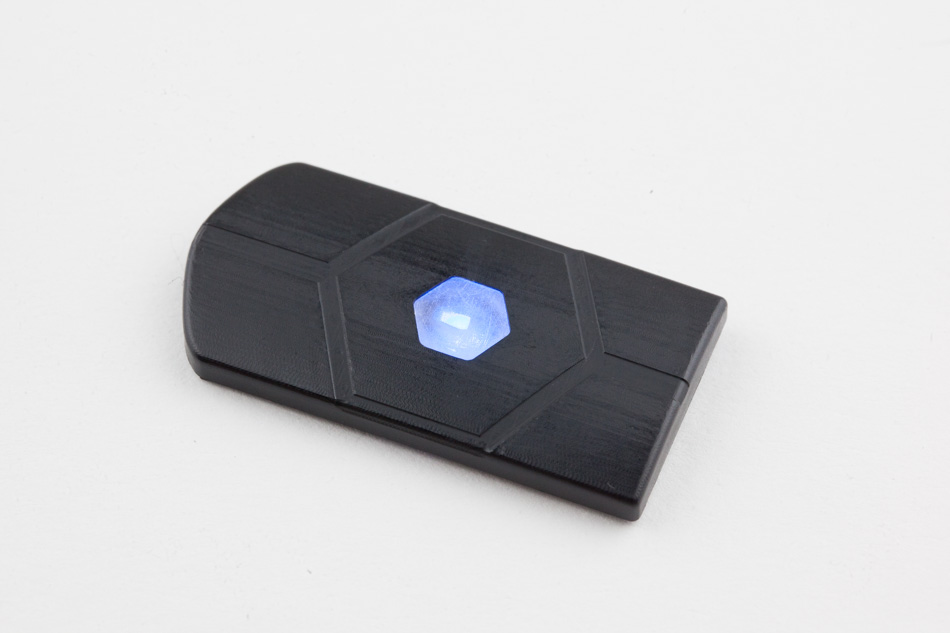
CNC machining can be a great choice for producing prototypes. While one-off prototypes can be very expensive, you can get huge cost savings when you start to move into larger quantities. Additionally, because CNC machining uses a solid block of material, the parts are functionally stronger than 3D printed parts, which are susceptible to fracturing along the build layers due to small voids in them.
Here’s an overview of best use cases for CNC machining as well as pros and cons to consider:
Best Uses for CNC Machining:
- Mid-stage prototyping
- Production models
- Ideal volume: 3+ units
Pros of CNC Machining:
- Functional parts/assemblies that can be tested just like production parts
- Strength consistent with end-use requirements
- Environmental resistance (temperature)
- Tight tolerances (up to 0.005”/0.0127mm)
- Variety of materials
Cons of CNC Machining:
- Requires more pre-production planning
- Is typically more expensive
- Produces more material waste
- Setup + CAM time costs
When Should You Switch from 3D Printing to CNC Machining?
There is no single rule for when to make the transition from 3D printing to CNC machining. At times, product development can benefit from both manufacturing methods.
For example, many aerospace companies require high-strength prototypes. So, they may do a quick 3D print to check size and form, then produce the same part using CNC machining for testing. They test, record the results, iterate on the design, and repeat the cycle.
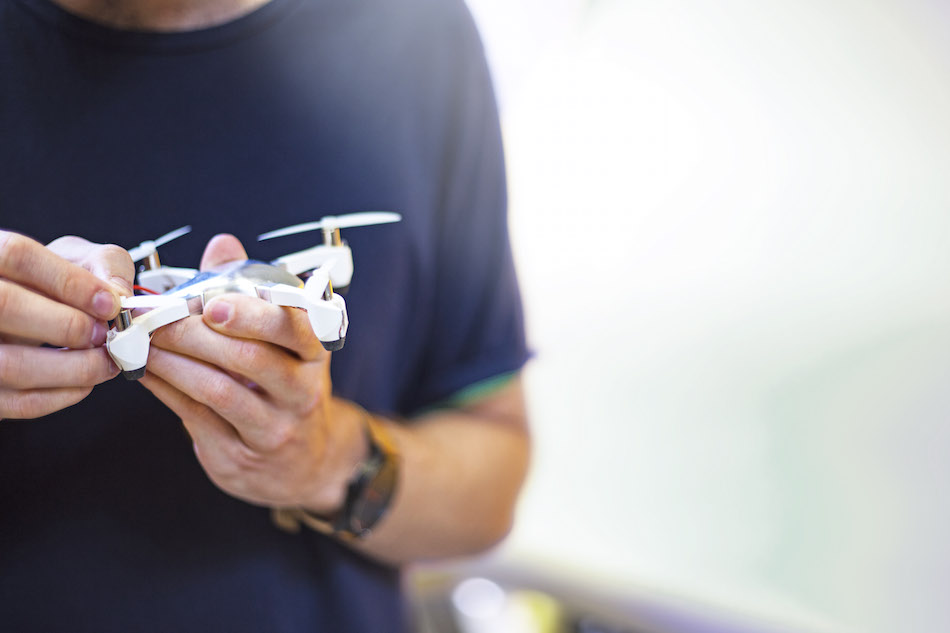
In most cases, however, you can look at your design maturity as a signal for when to move away from 3D printing and begin machining parts for functionality and strength closer to production materials.
To help you figure it out, here’s a quick design maturity checklist — if you answer yes to any of the following, it’s time to consider making the transition.
Design Maturity Checklist: Knowing When to Move from 3D Printing to CNC Machining
- Is your design far enough along that you are comfortable producing larger quantities?
- Have you stopped making significant design changes?
- Have you begun incorporating design for manufacturing?
- Do you need a higher level of consistency amongst parts?
- Do your parts have tapped holes?
- Are 3D printed parts not strong enough for your functional needs?
- Do you need to test your part in the final production material?
- Do you have certification requirements (eg. flammability, FDA, food-safe, FAA, etc…)?
Sometimes, 3D printed parts are machined in a hybrid approach. As parts come off the 3D printer, they can be fed to a CNC machine to get the part to a final stage with tighter tolerances and a more desireable surface finish. Combining 3D printing and CNC machining can improve the productivity of your CNC machining processes and reduce material costs.
Main Takeaways
Both 3D printing and CNC machining are critical tools in new product development. While 3D printing is quickly evolving as the go-to method to quickly take designs from a digital model to a physical prototype, CNC machining can’t be beat for functional prototype and production models.
Pro-tip: Keep an eye on the market where 2022 has brought some 3-in-1 CNC/3D Printer/Laser Engraver machines, so choosing the best manufacturing method may be as easy as a tool change!
Sourcing Simplified – Start Your Next Project With Fictiv
Fictiv is your operating system for custom manufacturing that makes part procurement faster, easier, and more efficient. In other words, Fictiv lets engineers, like you, engineer.
To learn more about our 3-day CNC machining services, check out our CNC machining service page — Fictiv is the ultimate partner who will provide you with precision CNC machined parts for prototyping and production runs.